Liquid Silicone Rubber (LSR) Parts Manufacturer
ISO 13485 and ISO 9001 certified, Precision Associates, Inc. (PAI) delivers close-tolerance, complex liquid silicone rubber (LSR) molded prototype and production components for the medical device industry. Customers benefit from rapid responsive service and extensive knowledge, resulting in a faster path to market.
LSR Applications
- Handheld devices
- Implantable devices
- Pacemakers
- Neurostimulators
- Urologic devices
- Drug delivery devices
- Monitoring equipment
- Operating room equipment
- Pumps
- Surgical instruments
- Ventilators
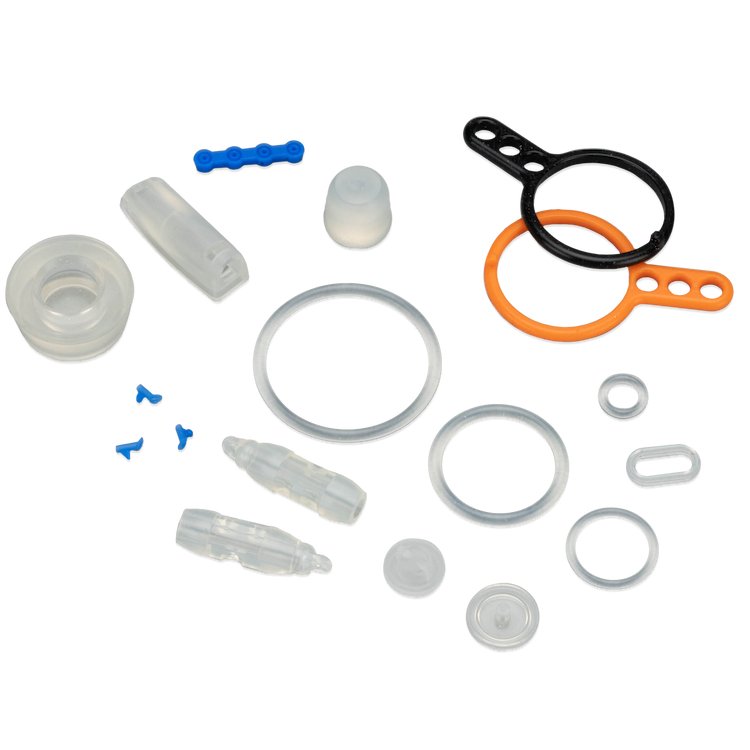
Material Formulation and Physical Properties
We use our extensive knowledge of additives to custom formulation LSR materials with physical properties, such as:
- Accurate versatility of shape and form
- Conductivity
- Excellent dimensional stability
- Excellent elongation
- Extended life cycles
- Fungus resistant
- High flexibility and durometer range of 20 to 80 Shore A
- Non-toxic
- Resistance to chemicals, water, acids, oxidizing chemicals, ammonia, isopropyl alcohol and others
- Superior insulation
- Thermal resistance from -155°F to 400°F
- Translucent and virtually any color
- Weather resistance, including UV light, ozone, o2, moisture and steam
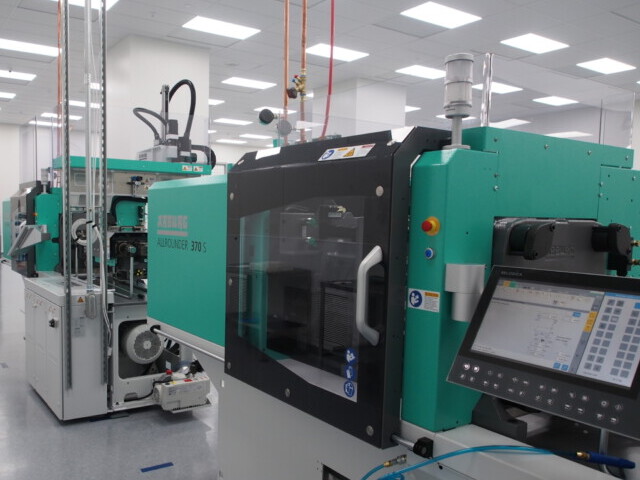
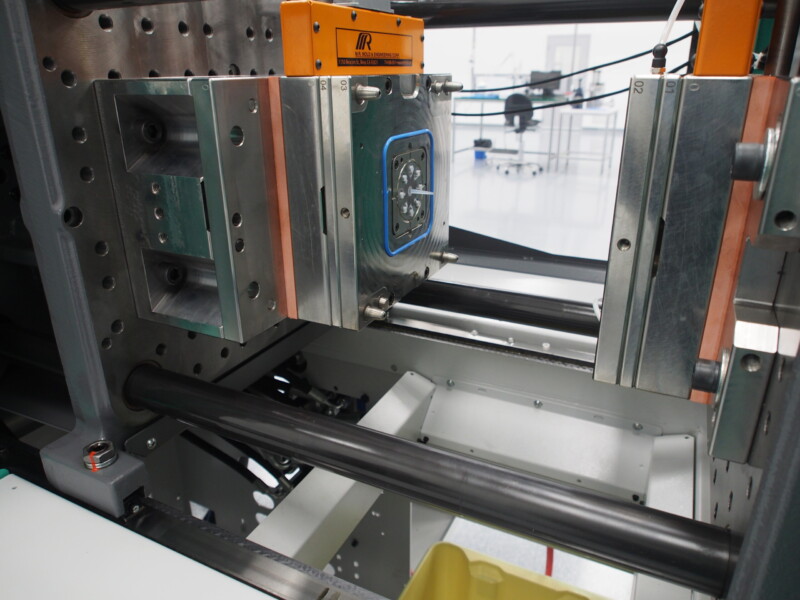
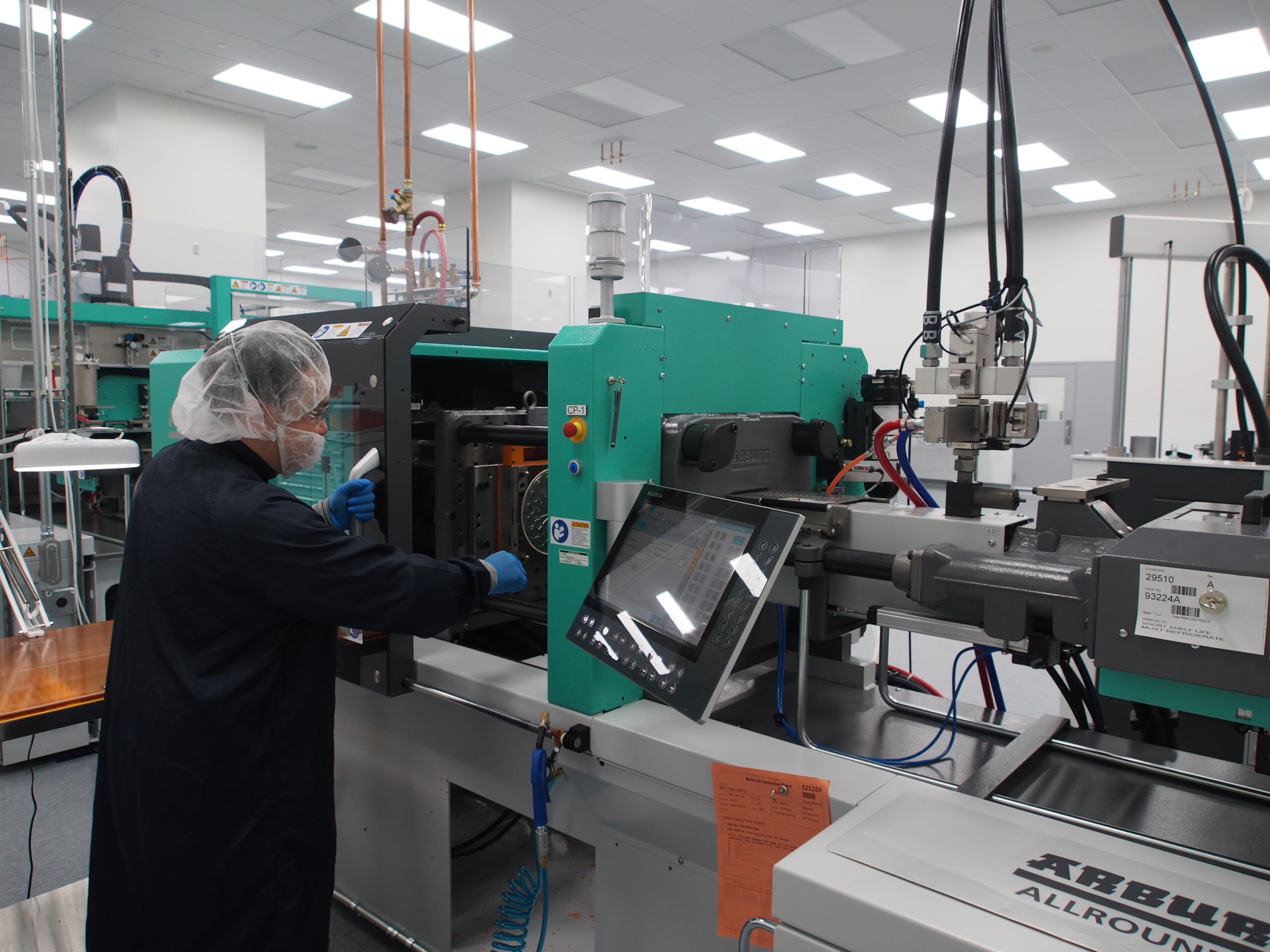
Turn Around Times
Depending on project scope, prototypes including the mold and parts can be manufactured in as little as three weeks. Production molds and process validation are completed often in eight to ten weeks. And production runs with existing tooling can be fulfilled in four weeks or more.
Tooling
Faster to machine and lower costs, prototype molds are constructed from mild tool steel. Production molds are constructed from 420 pre-hardened stainless steel (class 101). Often warranted for up to 1 million cycles.
Facility and LSR Manufacturing Equipment
Components intended for medical use can be produced in our 13,000-square foot Class 10,000 (ISO 7) cleanroom. All stages of LSR production from mixing compounds to packaging are performed within the clean room. PAI’s proprietary LSR molding process accurately produces quality parts and seals as small as 0.012 inches (0.30 mm).
Precision Associates has state-of-the-art equipment, including both vertical and horizontal LIM machines ranging from 28 to 70 tons with 240 to 600 kilonewtons of clamp force, fluid delivery and metering systems, robotic part tending and automated vision inspection is available.
100% Inspection
In addition to our standard 100% inspection, PAI often uses automated measuring equipment to ensure compliance to your specifications. LSR parts are shipped with PAI’s manufacturing cert, along with certification provided by our raw materials supplier, for full traceability.